Vulnerabilities in Digital Security Go Unnoticed amid Manufacturing Modernization, Pose Threats to Industries
The American manufacturing sector's rush towards modernization leaves its industrial backbone in peril. This precarious dance between efficiency and security stems from an unresolved issue: outdated industrial control systems (ICS) and SCADA networks, unprepared for an internet-connected world.
Case in point, a top-tier global manufacturer found its production facilities at risk when modernization efforts led to cloud-based analytics and remote monitoring integrations, unintentionally exposing multiple SCADA endpoints to the public internet. Lacking adequate authentication controls and segmentation, these systems became juicy targets for hackers, potentially enabling them to manipulate industrial processes, causing downtime and safety hazards.
It's not just factory workers who might be put in danger or valuable assets damaged but also the integrity of critical telemetry data. Unauthorized access could allow attackers to alter production parameters, resulting in faulty goods. On top of these operational concerns, cybersecurity missteps can result in severe penalties under industry standards like NIST 800-82 and IEC 62443 and significant reputational damage.
This is a clarion call for an industry gung-ho about digital transformation — one that might boost productivity but simultaneously creates vulnerabilities in systems never intended to interact with the outside world.
The Looming Danger Lurking in the Shadows
Imagine this: Industrial control systems controlling factories built for a time when physical security was adequate — when a locked door and a security guard could keep assets secure. Today, in our haste to modernize, we're connecting these same systems to the internet, often poorly secured cloud alternatives, and remote access tools.
In our aforementioned example, attackers could have easily seized control of factory equipment, endangering workers, disabling production, or worst-case scenarios. Shockingly, traditional security tools failed to detect these vulnerabilities, as they weren't designed to spot them.
This arresting oversight has become all too common in manufacturing, where the boundaries between operational technology (OT) and information technology (IT) are increasingly gray.
The Pitfalls of Traditional Security Measures
Despite applying conventional security measures such as vulnerability scanners and network monitoring, organizations often remain oblivious to their actual exposure. Just take the case of several major manufacturers, whose internet-facing OT assets were discovered during external scans. These neglectful oversights included exposed Programmable Logic Controllers (PLCs), Human Machine Interfaces (HMIs), and Remote Terminal Units (RTUs) directly controlling industrial processes. Internal security teams were blissfully unaware that these systems were open to the public internet.
These blind spots persist primarily because industrial networks evolve organically. Vendors install cellular modems for remote maintenance, or engineers set up temporary VPNs for remote monitoring that later become permanent. Traditional security tools overlook such vulnerabilities because they operate under outdated assumptions, scanning known networks, checking registered assets, and monitoring predefined systems. In today's fast-paced manufacturing environments, however, shadow OT and unmanaged connections proliferate, leaving dangerous gaps in security.
Seeing Industrial Control Systems Through an Attacker's Eyes
Manufacturers will need to fundamentally reconsider their approach to monitoring and securing their industrial systems. The conventional "inside-out" security approach, relying on internal network scans and predefined asset lists, is no longer sufficient. Instead, an "outside-in" approach examines a manufacturer's infrastructure from an attacker's perspective.
This outside-in approach has already shown promise in real-world applications. A major manufacturer, for instance, recently employed outside-in reconnaissance to survey its externally exposed systems using Open-Source Intelligence (OSINT) techniques akin to those hackers might deploy to find the best avenues into their organization. This feat identified multiple internet-facing industrial systems that traditional security tools had missed, including exposed SCADA endpoints controlling critical production processes, industrial protocol converters providing remote access, and human machine interfaces (HMIs) with default credentials still activated.
Action Plan
Enough chatter — here's what needs to be done:
Assess External Exposures
Start by scanning your infrastructure from the internet's perspective to identify any internet-facing industrial assets, such as controllers, HMIs, protocol converters, and remote access solutions.
Embrace Broad Discovery
Avoid confining security assessments to known assets or networks. Ensure a wide-ranging survey across all business units, subsidiaries, and acquisitions, seeking out "shadow OT" systems connected to the internet without security team awareness.
Test Thoroughly
Conduct thorough security testing of all exposed assets, not just the critical ones. Verify if they have default credentials, unpatched vulnerabilities, and insecure configurations specific to industrial systems.
Consider Impact, Not Just Technical Severity
Given security factors like operational dependencies, safety implications, and industry-specific regulatory requirements, evaluate which vulnerabilities to prioritize and tackle first.
Integrate Knowledge Widely
Communicate discovered exposures and the need for remediation to all relevant stakeholders, from security teams to operations personnel to executive leadership.
The Hard Lessons to Learn
Some argue that digital transformation's benefits surpass its risks in manufacturing, and they're right. But success hinges on prioritizing cybersecurity not just as an IT concern, but as a fundamental operational risk demanding leadership attention. The time to act is now. Secure these newly connected systems before attackers exploit them, and we learn these lessons the hard way.
- Unprotected SCADA endpoints, control systems, and industrial protocol converters are often left exposed due to the increasing digitization of manufacturing, posing significant risks to both workers' safety and production.
- Conventional security measures may provide insufficient protection in today's fast-changing manufacturing environment, where organic network growth and shadow OT systems create blind spots for traditional security tools.
- Adopting an "outside-in" approach to securing industrial systems by conducting internet-perspective scans and employing Open-Source Intelligence (OSINT) techniques can help manufacturers identify previously overlooked vulnerabilities, such as exposed SCADA endpoints and unauthenticated industrial control systems.
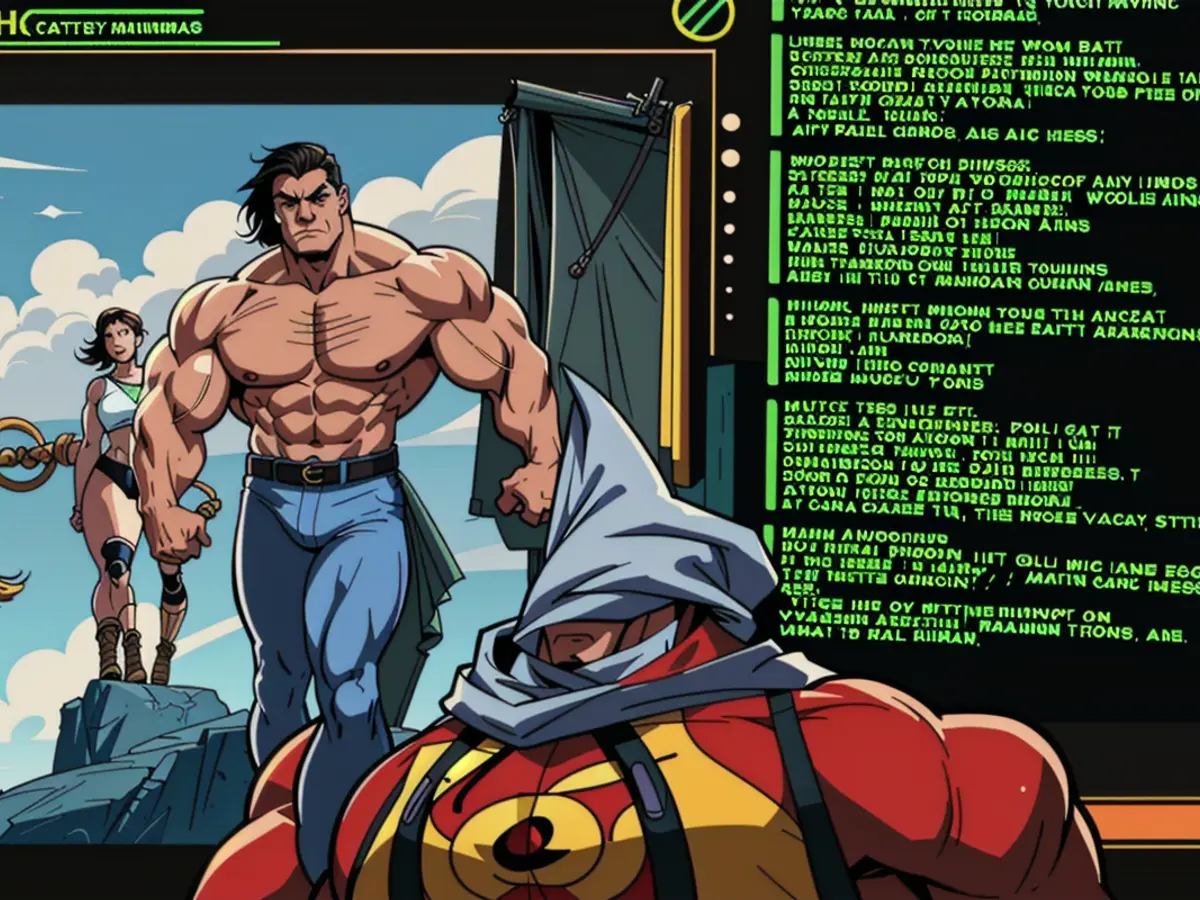
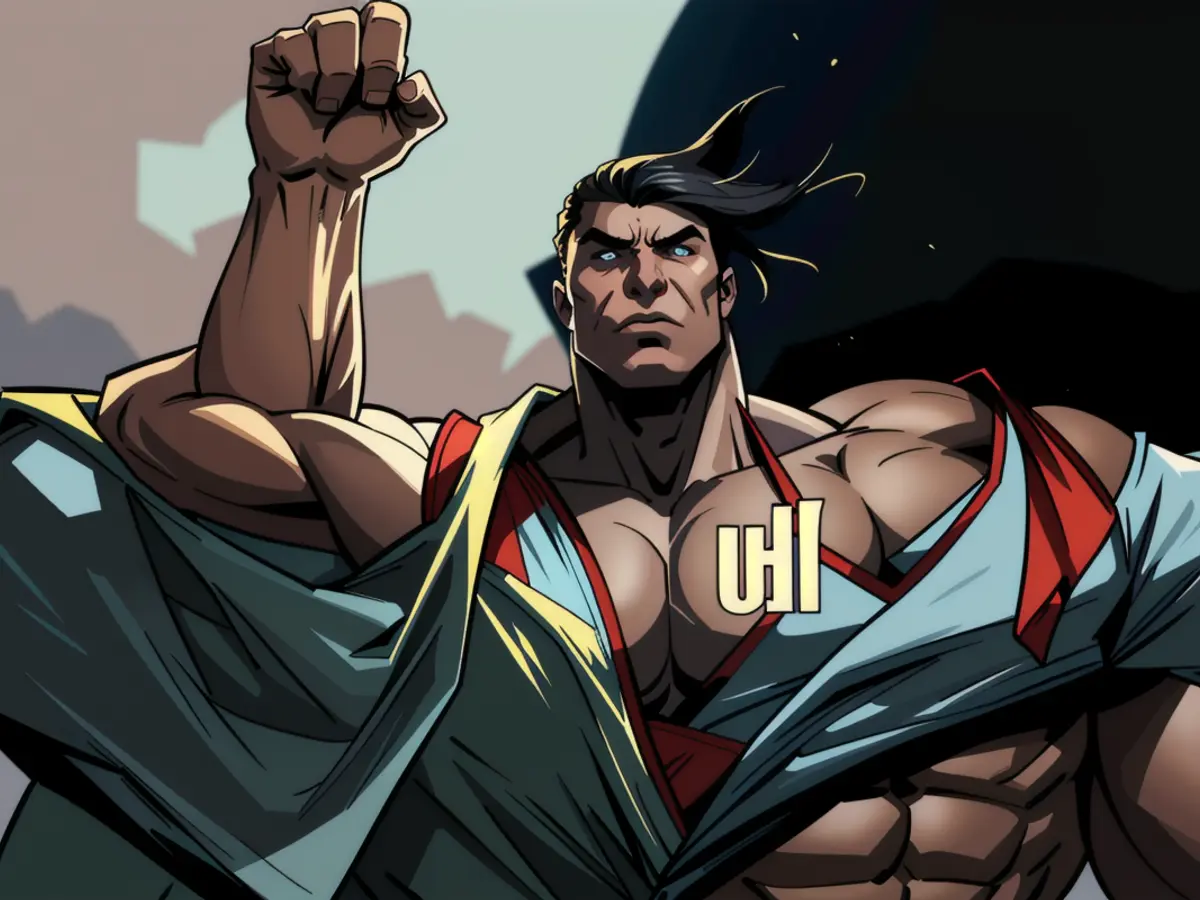
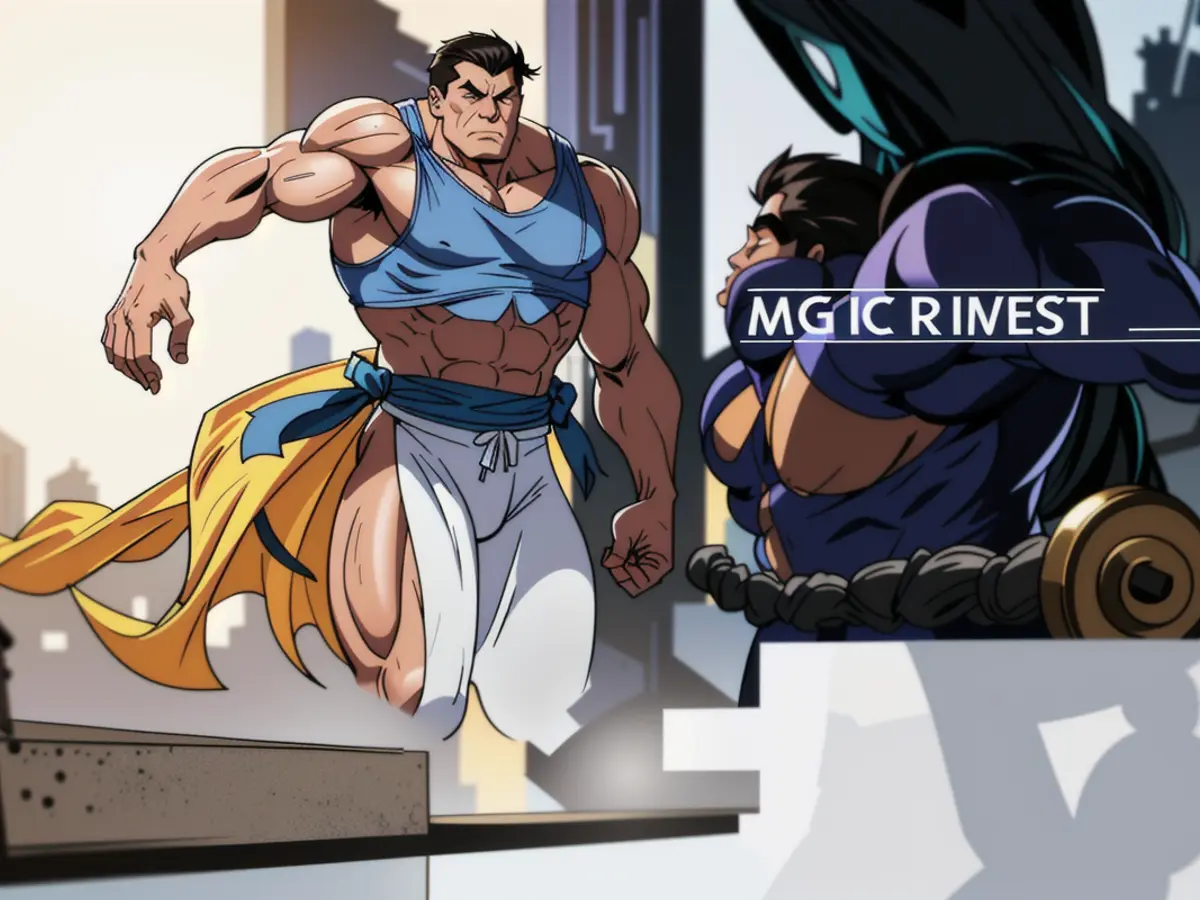